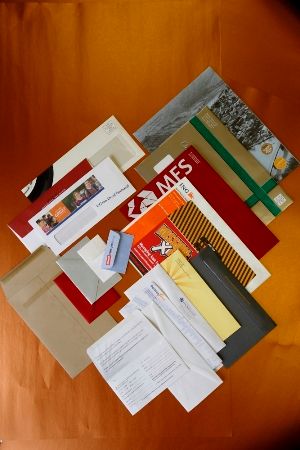
Graphic designers are the muse behind printers. They provide and execute the creative ideas which the printer then takes and brings to life on paper. In the new age of printing, designers must not only be creative but also adept at using the vector-based software and other digital tools necessary to provide a quality, print-ready image.
At Elite Envelope, we work with graphic designers all the time. Usually the designer will work for the customer to come up with the image they want and after the customer places the order, he will allow us to deal directly with the creative talent. Most times, we receive art files that are ready to go. However, sometimes that is not the case. The reasons can vary but the one I’ll focus on today has to do with practicalities.
Yes, I know that taking the practical approach is sometimes seen as the bane of the creative process. It involves all sorts of compromises and replaces the emphasis from the exciting “what is possible” to that ever more bland and boring “what is doable.” How many times did our parents tell us to “be practical”; advice we probably ignored to our eventual peril. And that’s the point – ultimately being practical is going to succeed far more than not. And while we love to read about those that figure out a way to get beyond all that, they are few in number so emulating them is just not, well…, practical!
One of the more common examples of this in the world of envelope printing has to do with heavy coverage that prints over the envelope seams or folds. When paper is folded, that area is relatively higher to what is on either side. Offset printing on envelopes is done with rollers that exert pressure on the printed surface. If the press is printing a solid which covers a fold, the result will be a white mark running directly down the fold itself. This is because of the different height of the folded area.
This is a pretty easy one to prevent by doing one of several things: You could simply move or shrink the solid so that it doesn’t cover the fold. Or you could use a screen of the color to make the solid lighter so that the white line would be less pronounced. Depending on the design and size of the mail piece, it may also be possible to switch from a diagonal seam envelope to a side seam which would provide a larger unfolded area for printing. You could also simply re-design or, if cost is not a major factor, print the envelope on a flat sheet and convert it after the fact which effectively elminates the problem altogether.
Ultimately, the process works best when the envelope printer is in touch with the graphic designer early in the process. That ensures a harmony between what can be done and what works best – beautiful music for all concerned!
Tell me about your envelope printing problems. I’d love to hear from you. Also, if you’re looking for free, expert advice on a future design, just e mail me through the website.