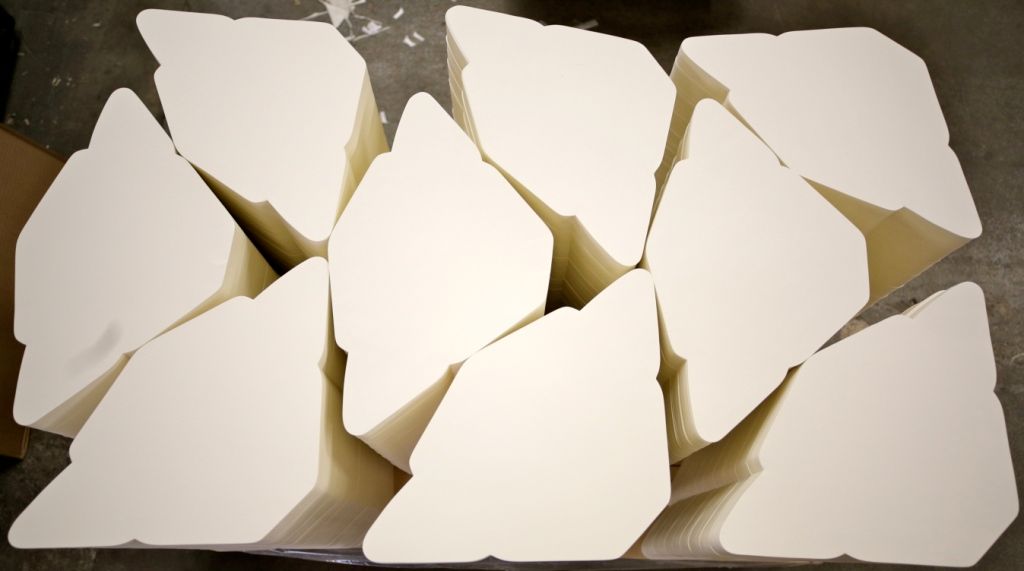
I hope everyone out there is doing OK and coping with the pandemic as best as possible. It’s still on the forefront of everyone’s mind obviously and will be for a while yet. However, life must go on and the small signs of economic recovery, at least relative to the depths of April and May are encouraging. Elite Envelope was deemed “essential” due to our connection to the mail, so we’ve been operating all throughout. It’s been an interesting journey, a challenging time, but we’re doing fine, and I hope you all are as well.
Today’s topic is one that comes up just about every day with envelope converters and envelope printers; i.e. what style of envelope is best for the customer’s particular application and why.
We recently got a quote request for 500,000, #10 standard window envelopes printed black on the face only. The best price for a job like that is based on flexo printing which is done in-line as the envelope is made. The most economical style or construction of the envelope at that quantity would be side seam. There are two reasons for this. First, side seam envelopes are generally produced on machines which use rolls of paper. The envelopes are cut out of the web paper roll as they pass through the converter and then printed. It’s a very efficient process. Diagonal seam envelopes must first be cut as a separate process. Then, the cut “blanks” (pictured above) are fed through the converting machine. This adds time and cost to the process versus the side seam method. Secondly, web envelope converting machines generally run at a faster rate which obviously also reduces the production cost.
However, another important factor in a job like this would be how they are going to be inserted and mailed. Generally, an order that size will be run through automated inserting equipment. The larger and more sophisticated inserting machines will be able to run with either side seam or diagonal seam envelopes. However, diagonal seam envelopes, because of the way they are constructed in the back panel, will generally insert better. This is especially true on smaller or older equipment. Desktop inserters will have fewer options for adapting to different styles of envelopes.
In this case, the customer said he needed diagonal seam envelopes which were going to be significantly more expensive than the side seam style. As an alternative, we were able to provide an option for Executive Style envelopes. These are also commonly referred to as V-flap because of the pointed flap. Executive Style envelopes were devised to simulate the diagonal seam construction but at the rough cost of a side seam envelope. They are produced on web equipment like side seam envelopes. However, they have a larger “throat” (the part of the back panel of the envelope that measures down from the flap score line) which causes them to run better in many inserters. Regular, die-cut diagonal seam construction still is optimum for just about any envelope inserting application. But the Executive Style can be a cost-effective alternative at larger quantities.
Let me know you experience with diagonal seam and side seam envelopes. And please feel free to send me any questions you might have on this or any other envelope topic.
We’ll get through this – in the meantime, take care!